Media
Science publishes Super Steel breakthrough
developed by HKU-led Beijing-HK-Taiwan team at low cost
25 Aug 2017
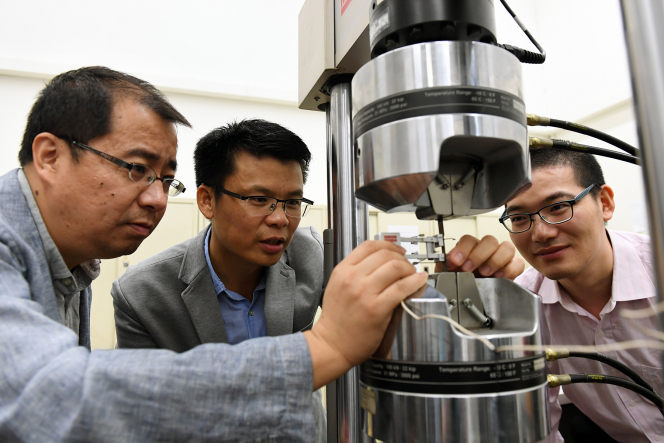
The research team uses a tensile machine to test the yield strength and elongation of steel. (From right): Dr He Binbin, Dr Huang Mingxin and Dr Luo Haiwen.
Automotive, aerospace and defence applications require metallic materials with ultra-high strength. However, in some particular high-loading structural applications, metallic materials shall also have large ductility and high toughness to facilitate the precise forming of structural components and to avoid the catastrophic failure of components during service. Unfortunately, increasing strength often leads to the decrease in ductility, which is known as the strength-ductility trade-off. For example, ceramics and amorphous materials have negligible ductility, although they have great hardness and ultra-high strength. To simultaneously increase both strength and ductility of metallic materials using conventional industrial processing routes is both of great scientific and technological importance and is yet quite challenging in both the materials science community and industry sectors.
A Beijing-Hong Kong-Taiwan mechanical engineering team led by Dr Huang Mingxin from the University of Hong Kong (HKU) has recently developed a Super Steel (also called D&P Steel as it adopted a new deformed and partitioned (D&P) strategy) which addressed the strength-ductility trade-off. Its material cost is just one-fifth of that of the steel used in the current aerospace and defence applications. This research breakthrough is recently published in the prestigious academic journal Science.
Steels have been the most widely used metallic materials in the history of mankind and can be produced with much higher efficiency than any other metallic materials. Therefore developing a strong and ductile breakthrough steel has been a long quest since the beginning of Iron Age in mankind history. In particular, it is very difficult to further improve the ductility of metallic materials when their yield strength is beyond 2 Gigapascal (GPa). Excitingly, a breakthrough steel – the Super Steel -- which has been developed by an HKU-led HK-Beijing-Taiwan team and published in the prestigious academic journal Science recently, is a successful attempt in realizing the above dream of achieving a high ductility above the yield strength of 2 GPa.
In addition to the substantial improvement of tensile properties, this breakthrough steel has achieved the unprecedented yield strength of 2.2 GPa and uniform elongation of 16%. Additionally, this breakthrough steel has two advantages:
(1). Low raw-materials cost.
The raw materials cost of the D&P steel is only 20% of the maraging steel used in aerospace and defence applications. The chemical composition of this breakthrough steel belongs to the system of medium manganese (Mn) steel, containing 10% manganese, 0.47% carbon, 2% aluminium, 0.7% vanadium (mass percent), and the balance is iron. No expensive alloying elements have been used exhaustively but just some common alloying compositions that can be widely seen in the commercialized steels. Figure 1 compares the raw materials cost between the present D&P steel with other high-strength steels.
(2). Simple industrial processing
The second advantage is that this breakthrough steel can be developed using conventional industrial processing routes, including warm rolling, cold rolling and annealing. This is different from the development of other metallic materials where the fabrication processes involve complex routes and special equipment, which are difficult to scale-up. Therefore, it is expected that the present breakthrough steel has a great potential for industrial mass production.
Compared with the widely used automotive steels (see DP780 and Q&P980 in Figure 2 below) as well as the steel used in aerospace and defence (maraging steel), the D&P steel demonstrated a much higher yield strength but maintaining a much better ductility (uniform elongation). The D&P steel also outperformed the nanotwinned (NT) steel which was also developed by the same HKU research team led by Dr. Huang Mingxin in 2015. Additionally, the developed D&P steel demonstrated the best combination of yield strength and uniform elongation among all existing high-strength metallic materials. In particular, the uniform elongation of the developed D&P steel is much higher than that of metallic materials with yield strength beyond 2.0 GPa (see Figure 3 below).
The development of this breakthrough steel is a successful example of collaboration of young scientists from Hong Kong, Beijing and Taiwan. This collaboration is led by Dr Huang Mingxin’s group from the Department of Mechanical Engineering of the University of Hong Kong (HKU). Dr Huang Mingxin’s group has been dedicated to study the deformation mechanism of ultra-high strength metallic materials. In this research, Dr Huang’s group firstly proposed a new deformation mechanism that the high dislocation density can improve both strength and ductility simultaneously. It is worth mentioning that a general belief in textbooks is that increasing dislocation density will elevate the strength but undesirably deteriorate the ductility. Dr Luo Haiwen’s group from University of Science and Technology Beijing is specialized in steel processing and has successfully introduced high mobile dislocation density in this breakthrough steel. Dr Yen Hung-wei’s group from National Taiwan University supported this new deformation mechanism by performing the advanced microstructure characterization (see Figure 4 below).
The research outcome is a collective contribution from young scientists in the University of Hong Kong, University of Science and Technology Beijing, National Taiwan University and City University of Hong Kong and it has been published in the prestigious journal Science on 24 August 2017 with a title of “High dislocation density induced large ductility in deformed and partitioned steels”. The first author of this paper is Dr He Binbin who is currently a post-doctoral fellow in Dr Huang’s group. The corresponding authors are Dr Huang Mingxin from the University of Hong Kong and Dr Luo Haiwen from University of Science and Technology Beijing. The complete author list is as below: B.B. He, B. Hu, H.W. Yen, G.J. Cheng, Z.K. Wang, H.W. Luo, M.X. Huang.
Figure 1 The raw materials cost of the present Super Steel (D&P steel) as compared with other high strength steels.
Figure 2 Tensile properties of the present breakthrough D&P steel compared with other high-strength steels, including maraging steel, nanotwinned (NT) steel, quenching and partitioning (Q&P980) steel and dual-phase (DP780) steel.
Figure 3 Yield strength and uniform elongation of the present breakthrough D&P steel compared with those of other existing high strength metallic materials. D&P steel demonstrated the best combination of yield strength and uniform elongation.
Figure 4
(a) Electron backscatter diffraction (EBSD) phase image showing the lamella microstructure of layered austenite grains embedded in tempered martensite matrix.
(b) The dislocation structures in martensite as enlarged in transmission electron microscopy (TEM) image.
(c) TEM image showing the elongation of dislocation cell structure after the 8% tensile strain.
(d) TEM image confirming the transformation of metastable austenite to martensite after 16% tensile strain.
For the powerpoint slides about this research, please click here. (Please credit “The University of Hong Kong”)
Media enquiry
Communication and Public Affairs Office Ms Rhea Leung (Tel: 2857 8555/ 9022 7446; email: rhea.leung@hku.hk)